28. April 2020 Das Dach wird komplettiert
Hallo zusammen,
weiter geht's wie versprochen mit Lüftern, Griffstange, Schlussscheiben-Haltern und der Aufstiegsleiter. Als erstes zu den Lüftern. Wie schon beim Pwl02 ist hier ein Lüfter außermittig, daher muss der schon mal zuerst identifiziert werden. Insgesamt sind es 5 Lüfter, die auf das Wagendach gelötet werden müssen. Es ist von Vorteil, wenn man die Angüsse nur etwa 1-1,5mm lang läßt. Sollte wie bei mir der Anguss-Vierkant noch zu groß für die vorhandenen Bohrungen sein, ermittelt man das Eckmaß des Angusses und bohrt die Löcher im Dach einfach auf. Danach kann man die Lüfter der Reihe nach auflegen, vorher Lötwasser aufs Dach und zwei Stück Lötzinn beidseitig dazu und dann von außen zuerst den Lüfter und zum Schluss das Dach erwärmen bis das Lot geschmolzen ist. Geht recht einfach.
Für Griffstange und Schlussscheiben-Halter sind die Bohrungen im Dach bereits vorhanden. Dadurch ist das Anlöten dieser Teile einfacher und kann erst später durchgeführt werden. Somit zuerst zur Aufstiegsleiter. Die ist beim CL14 auf der gleichen Plattformseite wie die Handbremse auf der rechten Seite. Ich hatte ja schon beim Pwl02 eine Änderung am Teil vorgenommen, auch hier entspricht das Gußteil nicht dem gebrauchsfertigen Zustand. Der Haltewinkel mit der Schraubenimitation zeigt zur falschen Seite und damit würde der Zugbegleiter beim Aufstieg drüberstolpern. Das geht natürlich so nicht!
Den Haltewinkel einfach auf die andere Seite biegen wäre möglich, man büsst dann allerdings die Schraubenimitation ein und hat das Risiko dass der Halter später abbricht. Daher habe ich den Haltewinkel oben am Bogen abgeschnitten und mit Silberlot wieder richtig rum hart angelötet. Aufgespannt habe ich das so:
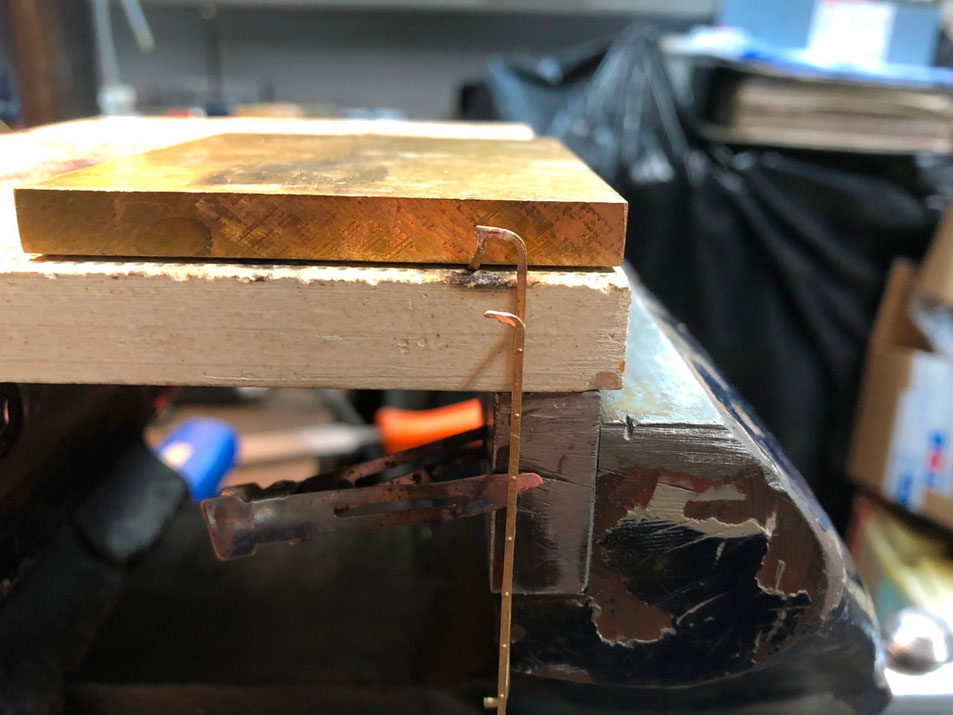
Für solch kleine Teile reicht auch die Temperatur des Lötbrenners aus, um ein 600 Grad Silberlot zum Schmelzen zu bringen, ohne dass das Messing davonläuft. Keine Angst vor dem Hartlöten! Wenn Flussmittel und Silberlot zusammenpassen, funktioniert das super! Vielleicht zeig ich das mal am ARGE Stand bei einer der nächsten Ausstellungen. Würde man das Teil weichlöten, dann geht es beim Anlöten des Winkels am Dach garantiert wieder auf. Das wäre dann "Modellbauer ärgere Dich nicht" und das brauchen wir nicht!
Nun zum Anlöten der Leiter: Die darf hier nur am Dach befestigt werden, die unteren Stützen müssen oberhalb des Puffers nur aufliegen, sonst kann man den Wagenkasten nicht mehr vom Fahrgestell trennen. Der linke Holm ist kürzer und wird nach dem Ausrichten und festklammern der Leiter an der Plattform auf der Dachunterseite festgelötet:
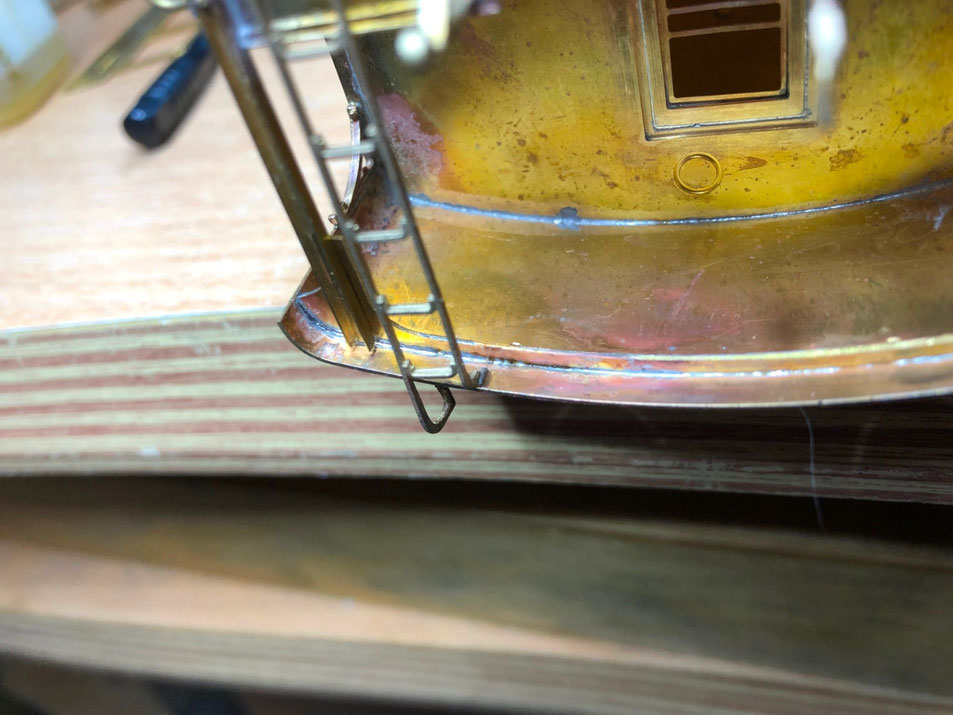
Danach noch mal die Lage der Leiter überprüfen und dann den Haltewinkel des rechten Leiterholms am Dach anlöten. Nun kann man die Griffstange und die Schlussscheiben-Halter in die dafür vorgesehenen Bohrungen einlöten. Die Schlussscheiben-Halter müssen nun noch in die richtige Lage gebogen werden, dann sieht das Dach so aus:
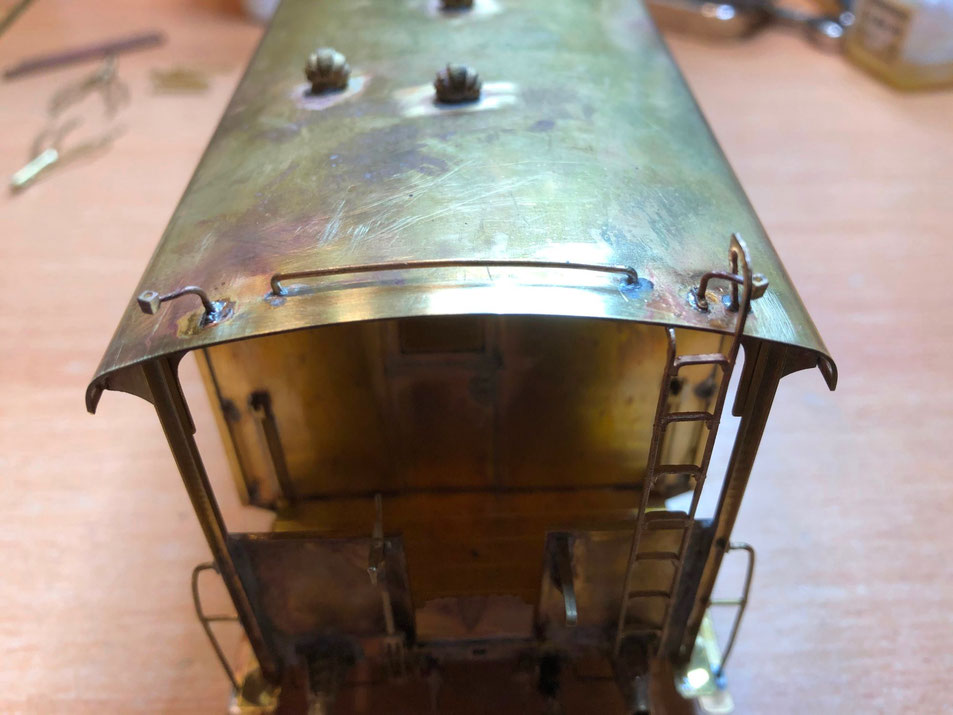
Kleiner Nachtrag: Die äußeren Spanten des Dachs habe ich doch tatsächlich zu beschreiben vergessen, das funktioniert aber genauso wie beim Pwl02, auch wenn die Spanten hier exakt passen und nur noch festgelötet werden müssen. Erst wieder mit Haarklammern an den Plattformstützen festklammern, dann in der Mitte heften. Dann den Wagenkasten abheben und die restliche Naht links und rechts ziehen. Das separat Löten der Spanten ist notwendig, damit die Plattformstützen nicht versehentlich mit festgelötet werden. Auf diesem Bild erkennt man den Spant recht gut, leider habe ich kein anderes Foto:
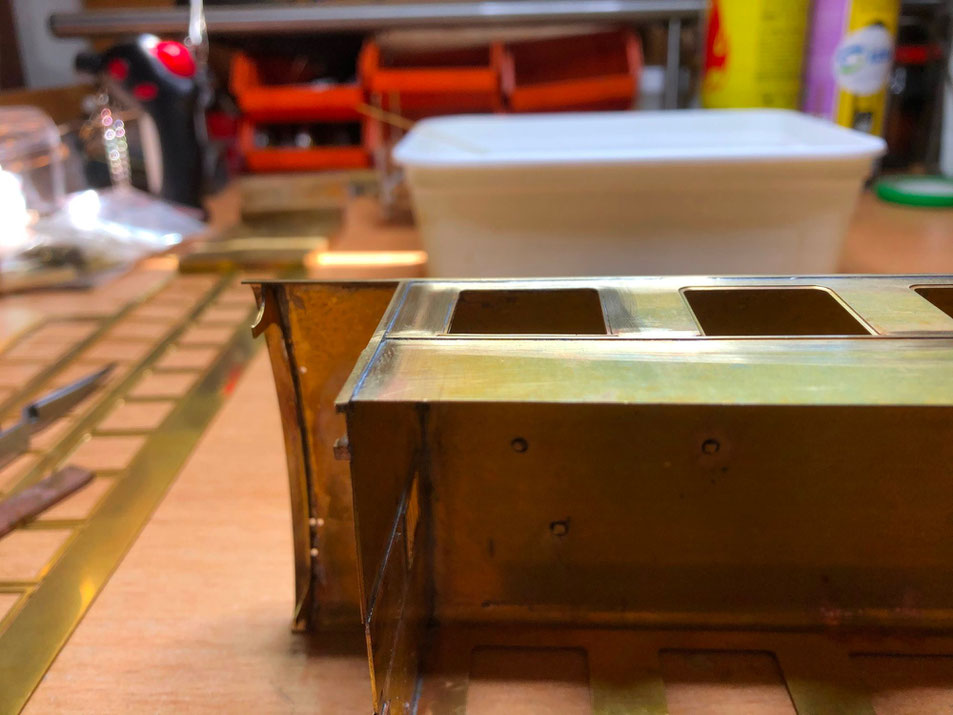
Zur Komplettierung des Karosserie-Rohbaus fehlen jetzt noch die Plattformgitter und die Übertrittssperre zwischen den Geländern. Dazu im nächsten Bericht.
28. April 2020 Die Plattformgitter und die Übergangssperre
Hallo zusammen,
jetzt wird's filigran! Die Plattformgitter am Wagenkasten festzulöten wäre der einfachste Weg, allerdings habe ich ja bis jetzt alle notwendigen Veränderungen durchgeführt, um den Wagenkasten z.B. für den Einbau eines Decoders oder zur Ausrüstung mit Fahrgästen wieder abmontieren zu können. Daher kommt das nicht in Frage.
Also müssen die Auflager mit der Griffstange mit einer 0,5mm Bohrung versehen werden, um dort die oberen Gitterträger einhängen zu können. Dazu habe ich die Lagernut mit einer PUK Säge vor dem Verlöten am Plattformgeländer noch etwas tiefer gesägt, damit sich der Gitterträger auch leicht bewegen lässt. Das Teil sieht vor dem Verlöten dann so aus:
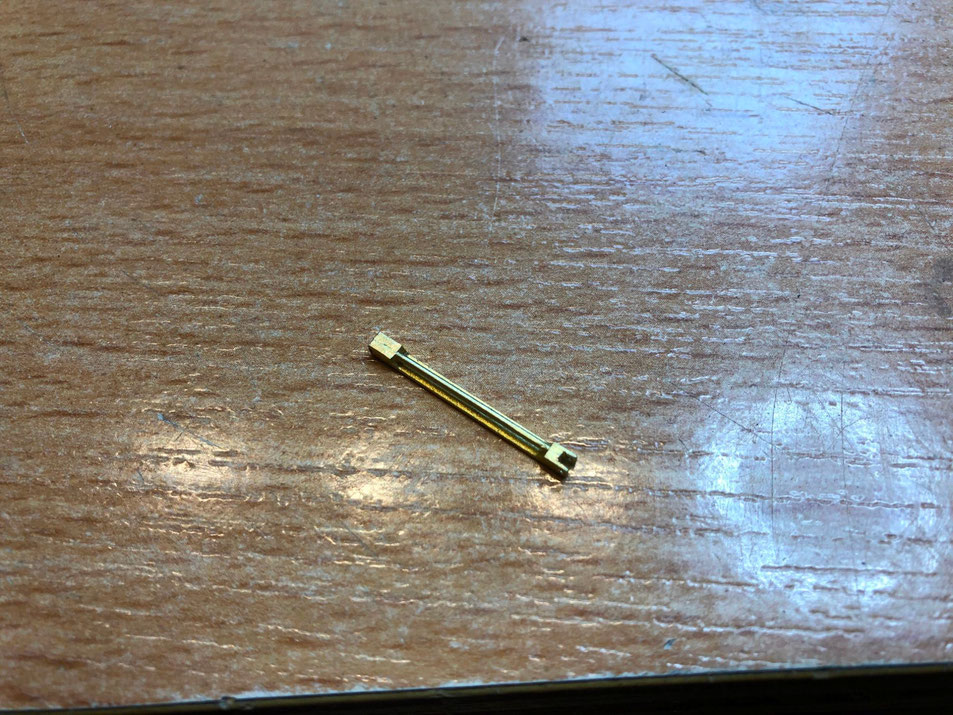
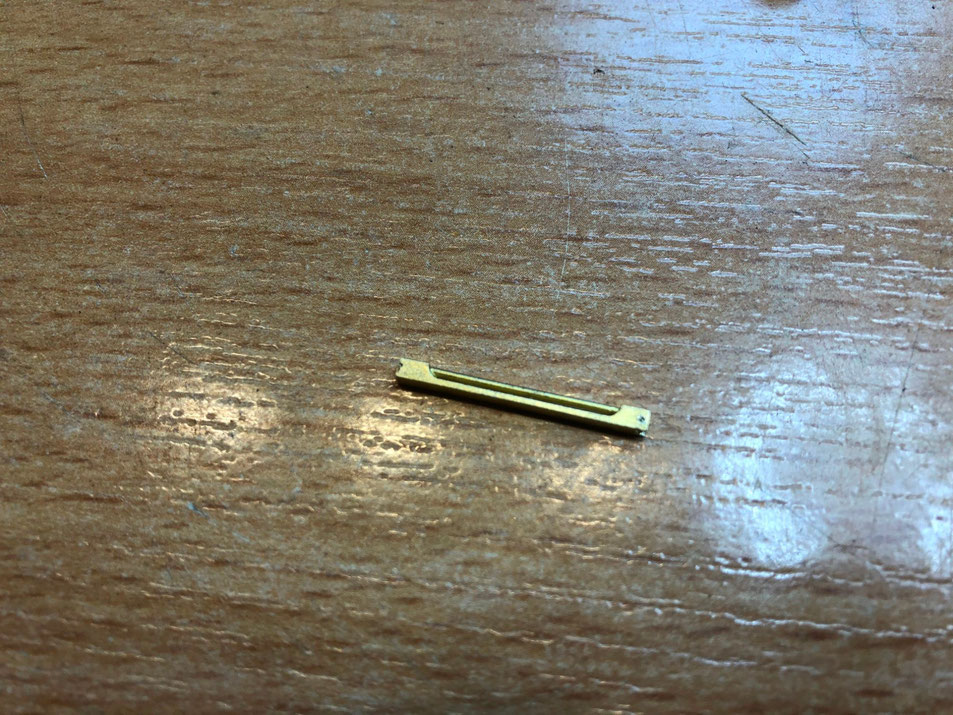
Jetzt können die Auflager an der Plattform angelötet werden. Das würde ich beim nächsten Mal schon beim Aufbau des Fahrgestells machen. Festgespannt habe ich es so:
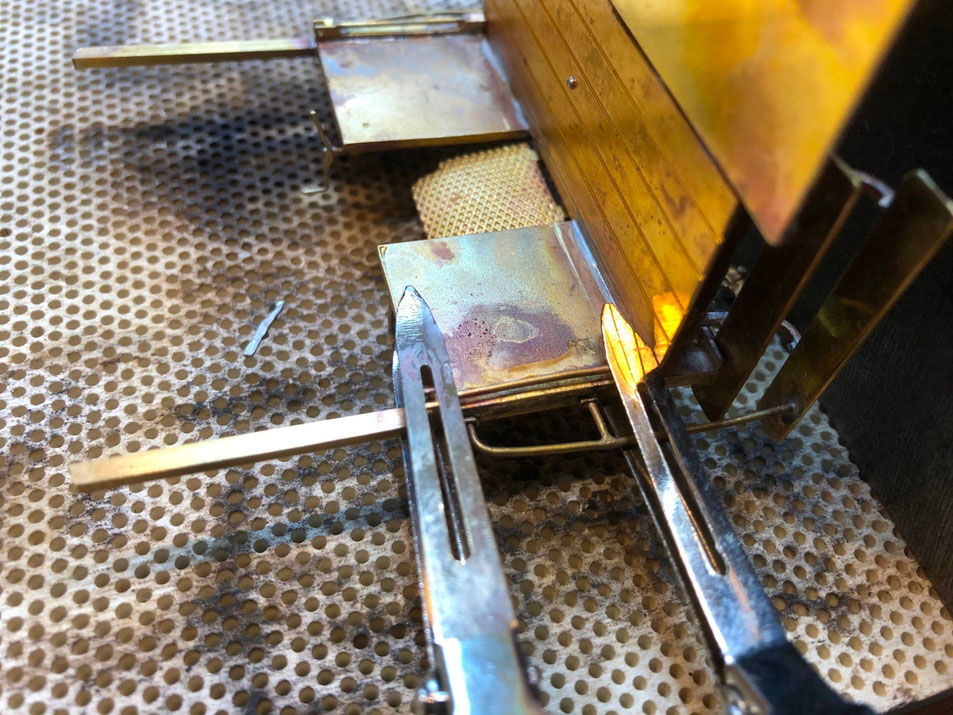
Mit der Flamme habe ich hier die Mitte des Geländers angepeilt und erst im letzten Moment auf das Auflager geschwenkt. So ist das Risiko, dass sich Teile ablösen, am geringsten. Es ist alles gutgegangen, deshalb können wir nun die oberen Gitterträger bearbeiten:
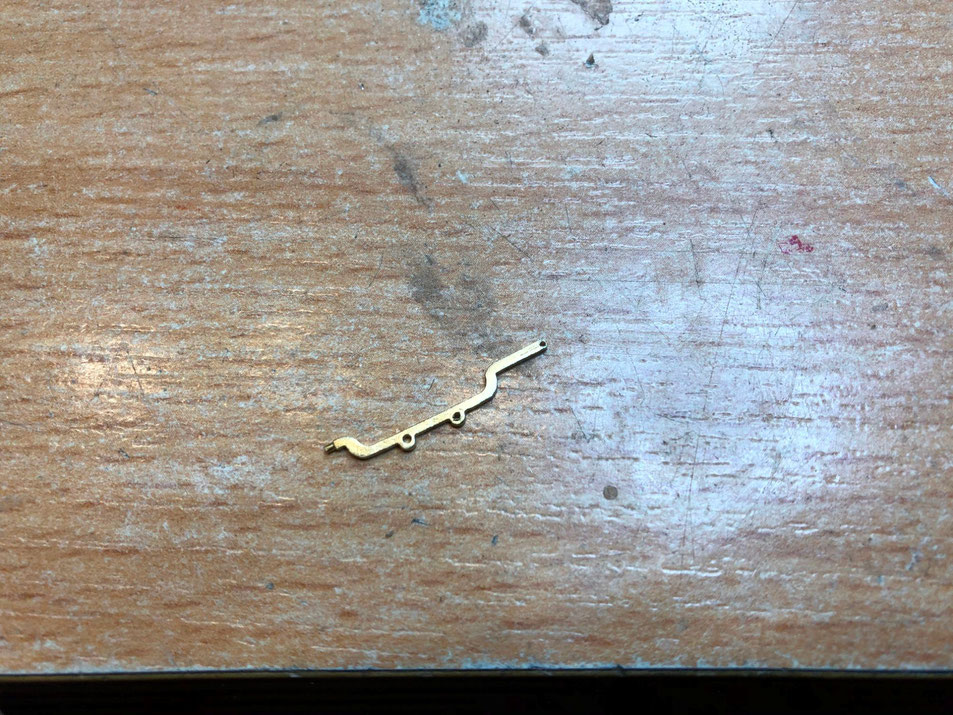
Auf dem Bild ist die zusätzlich eingebrachte 0,5mm Bohrung für die Lagerwelle zu sehen. Die erste Passprobe ergab folgendes Ergebnis:
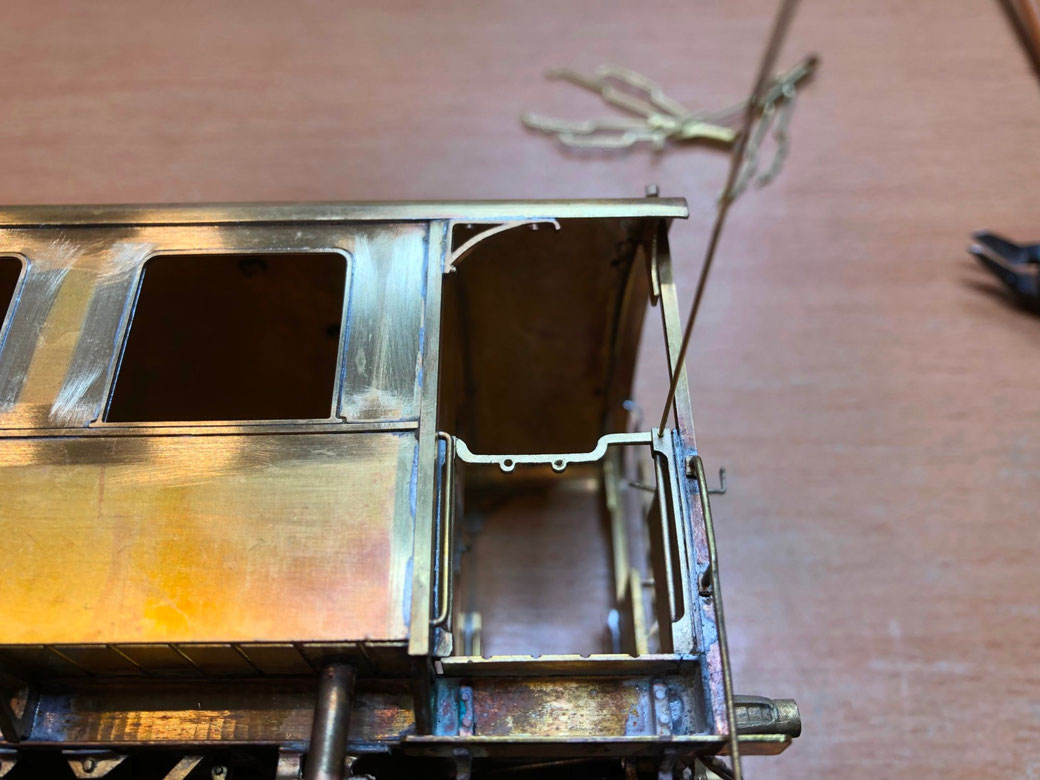
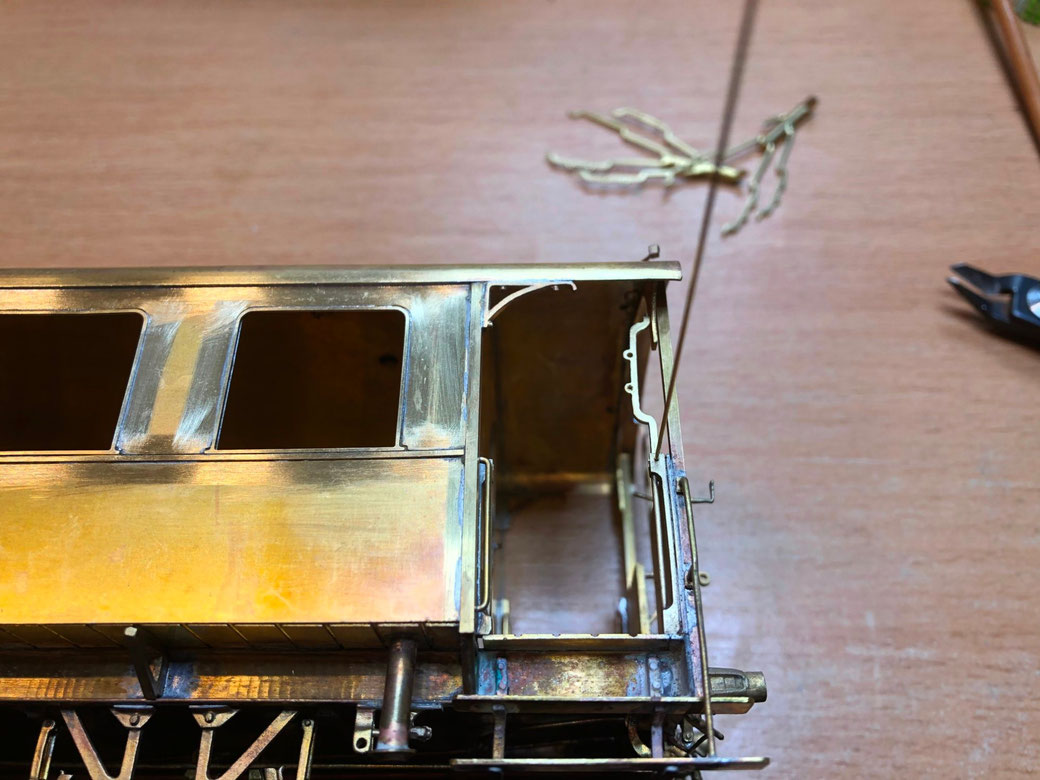
Das war schon mal der erste Erfolg, jedoch kam auch gleich das nächste Problem beim Versuch, die Gitterstäbe an den Gitterträgern zu befestigen: Die Bohrungen für die beiden Gitterstäbe dieses Teils haben ca. 0,9mm Durchmesser. Einen Messingdraht mit 0,8mm zu verwenden, war mir zu klobig, wenn dann sollte es ein 0,5er sein. Aber da war ein Problem: Ich konnte den 0,5er Draht zur nicht mehr lösbaren Montage auf der Rückseite nicht soweit flachdrücken, dass sich der Gitterstab nicht mehr lösen kann. Es hat eine zeitlang gedauert, bis ich auf die richtige Lösung kam. Zuerst habe ich kleine Beilagscheiben aus 0,3er Messingblech mit einer 0,5mm Bohrung versehen, in Form geschnitten und dann versucht, die kleine Scheibe auf der Rückseite festzulöten. Schon beim zweiten Versuch habe ich trotz Seidenpapier den Gitterstab am Gitterträger festgelötet. Das Gepfriemel war nicht "serientauglich". Dann hatte ich die Idee: Ich habe einfach die Bohrungen mit dem SMD Lötkolben zugelötet und mit 0,6mm wieder aufgebohrt. Jetzt klappte das Flachdrücken auf der Rückseite!
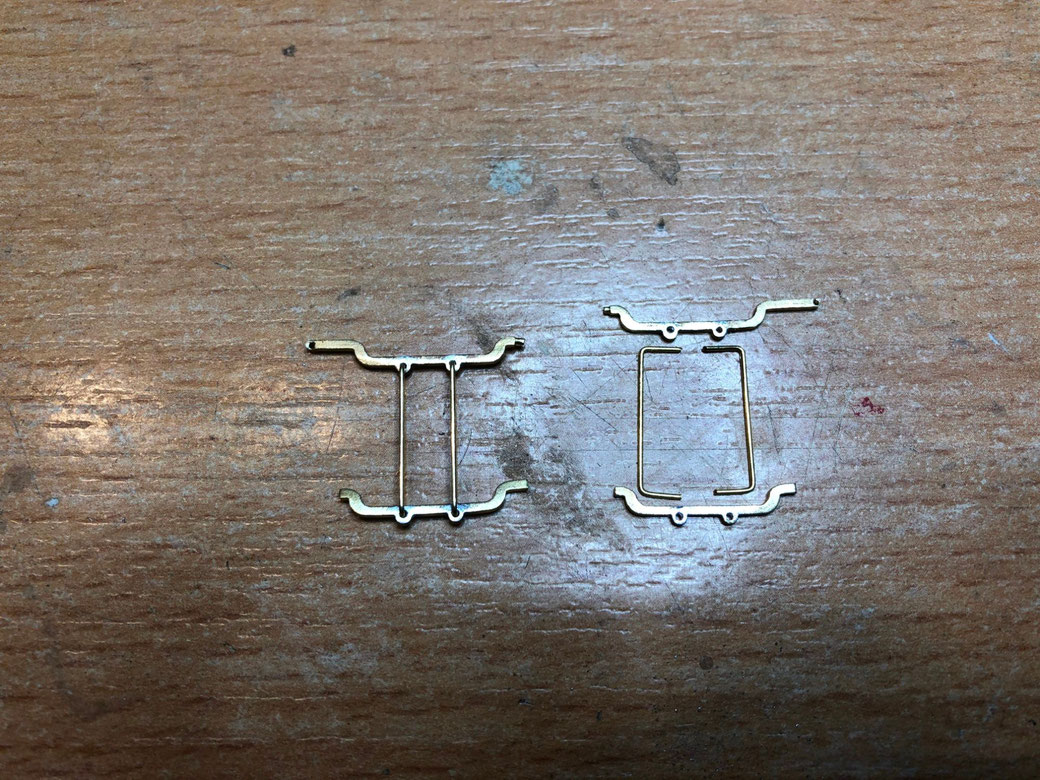
Eins muss ich noch erwähnen: Um den unteren Gitterträger richtig zu befestigen müsste man ein anderes Teil aus das vorhandene Auflager einsetzen, um ein unteres Lager zu haben. Dieser Aufwand ist zu hoch. Daher habe ich die unteren Gitterträger so gekürzt, dass sie zwischen den Auflagern frei pendeln können. Das ist für mich ein tragbarer Kompromiss. Geschlossen sieht das Gitter dann so aus:
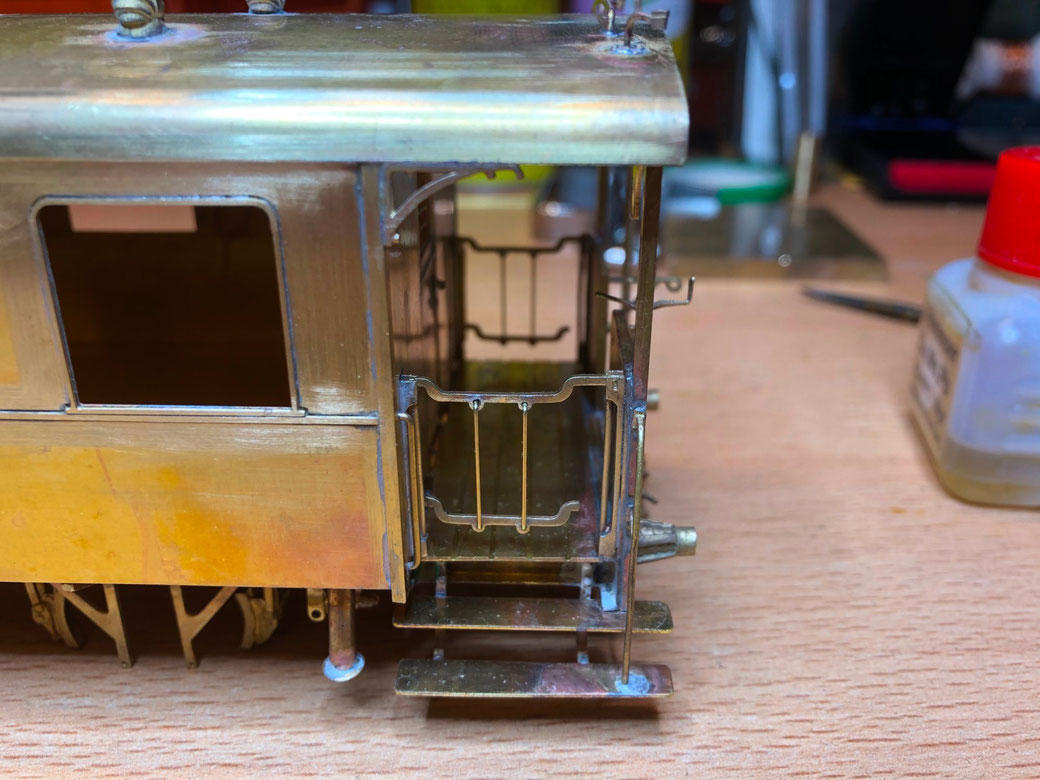
und offen so:
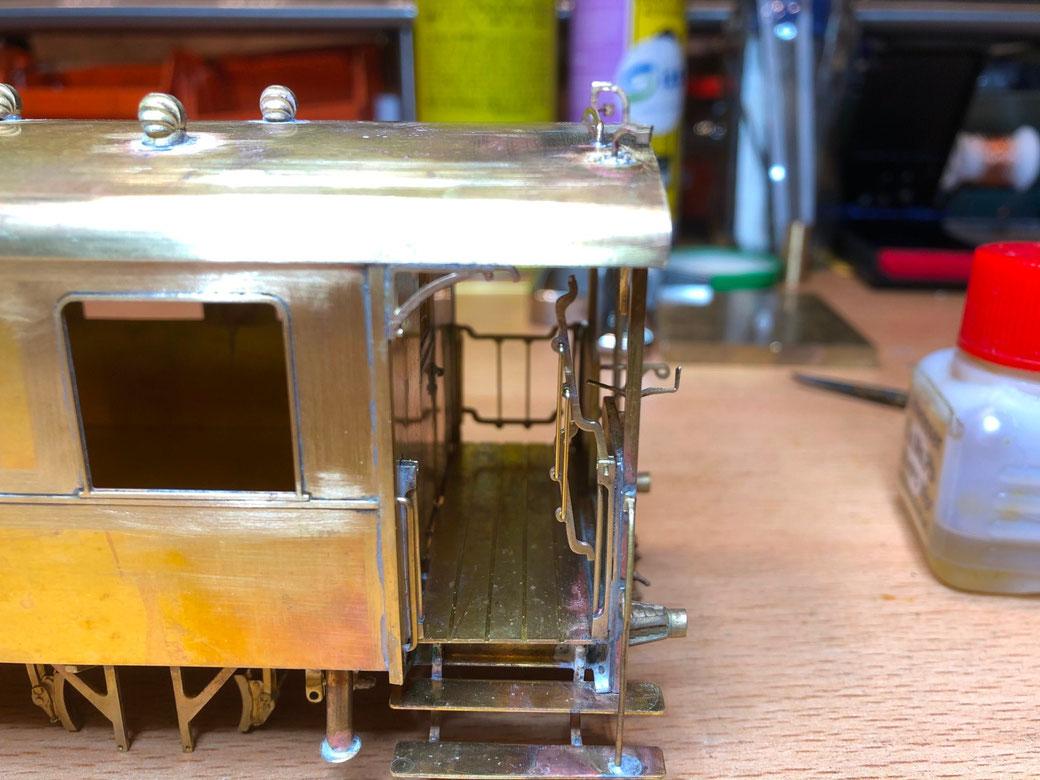
Der Bericht hat nun schon sehr viele Fotos, ich spendiere daher der Übertrittssperre einen eigenen Bericht.
28. April 2020 Die Übergangssperre
Hallo zusammen,
nach der Filigranarbeit mit den Plattformgittern jetzt noch die Übergangssperre zwischen den Geländern. Auch hier wäre das Festlöten eines U-Profils die einfachste Lösung. Andererseits: Es muss doch auch beweglich gehen! In meinem Fundus habe ich ein Rechteck-Messingrohr mit 4x2mm gefunden, das ich der Länge nach geteilt habe und so zwei U-Profile 2x1,5 erhalten habe. Die 0,5mm sind der Verlust durch die Sägeblattbreite. Dann habe ich das Teil so bearbeitet:

Die Lagerbohrung ist diesmal eine mit 0,7mm Durchmesser. Mein Vorrat an 0,5 und 0,6mm Bohrer ist leider aufgebraucht und bis Nachschub eintrifft, wollte ich nicht warten. Es geht aber auch so. Wie ich die 0,7er Bohrung für die Lagerwelle in das Plattformgeländer gebracht habe, zeige ich euch lieber nicht. Gott sei Dank ist dem fertigen Fahrgestell nichts passiert! Auch das wäre für ein späteres Projekt ein Verbesserungsvorschlag diese Bohrung schon am Einzelteil einzubringen! Es ist ein netter Gag und man könnte den Schaffner mit geöffneter Sperre auf der Plattform platzieren.
Sowohl bei den Gittern als auch bei den Sperren habe ich vorerst zur Befestigung nur jeweils Drahtstückchen eingesteckt, weil ich diese Teile zum Lackieren wieder entfernen möchte/muss. Erst danach werde ich richtige Schraubenimitationen einkleben. Da die Teile möglicherweise nach dem Lackieren nicht mehr so gut beweglich sind, werde ich zumindest die Gitter versuchsweise brünieren. Es wird sicher nicht schaden, wenn nicht alle Teile im gleichen Tiefschwarz lackiert sind.
Die Sperre sieht dann montiert und geschlossen so aus:
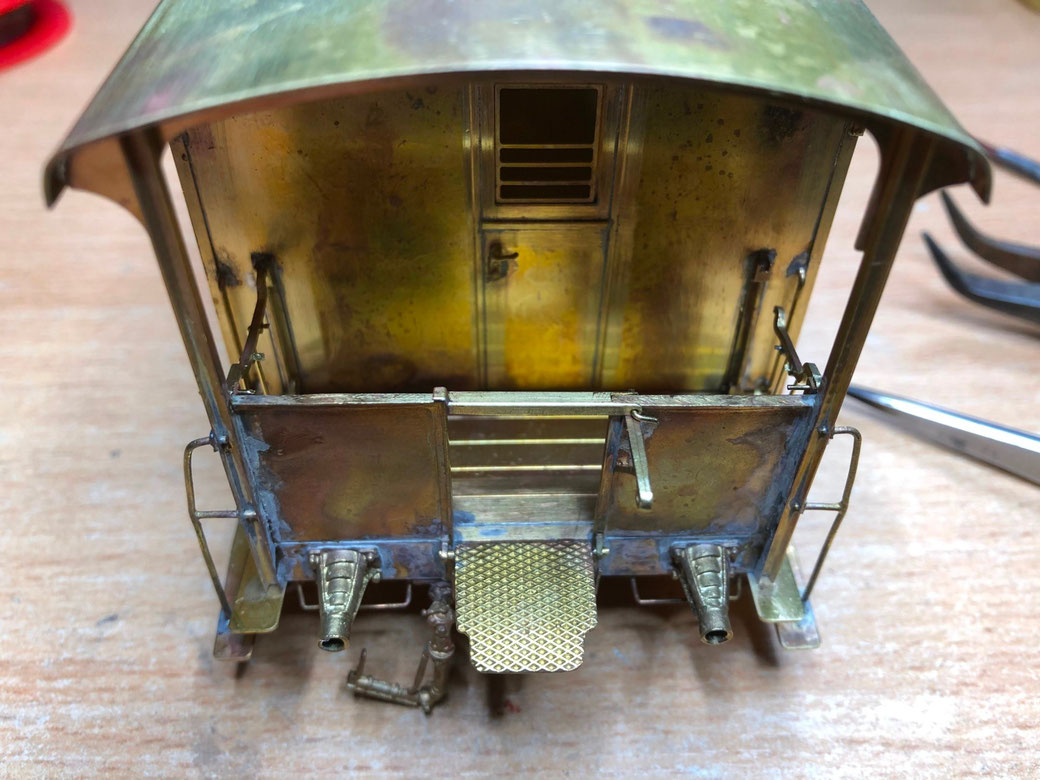
und offen so:
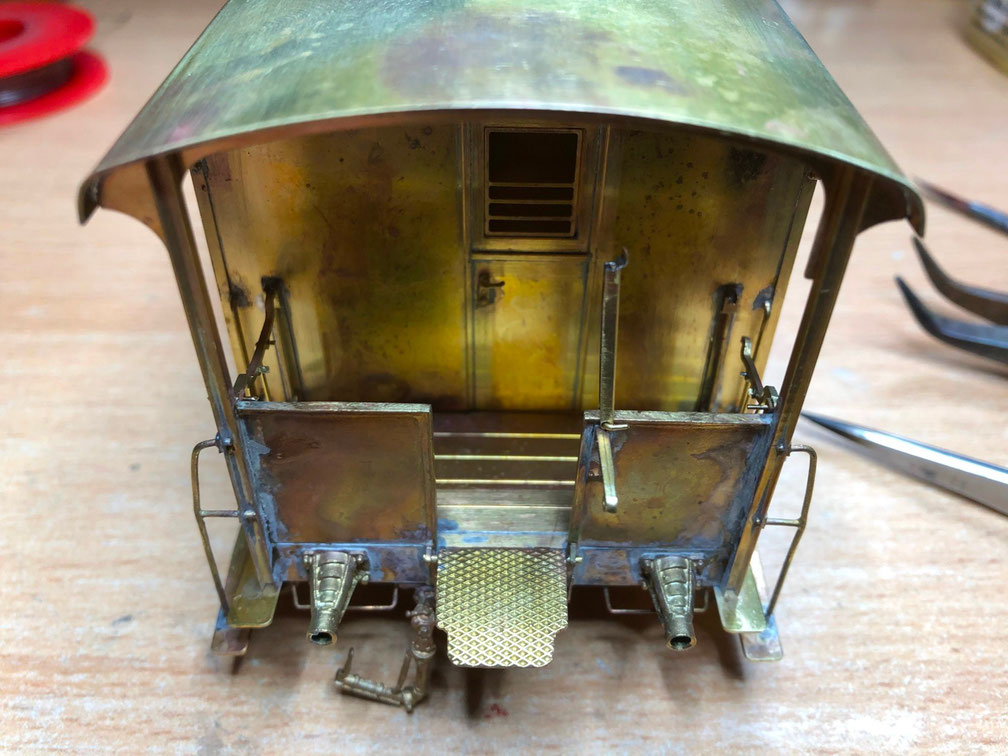
Wem die abgewinkelte Form des Gegenlagers aufgefallen ist: Das musste ich so machen, weil die die rechten und linken Geländer-Gussteile nicht gleich hoch sind und die Sperre auf jeden Fall parallel zur Plattform sein sollte. Ich tröste mich damit, dass das ganze dann interessanter aussieht.
Damit ist der erste CL14 karosseriebautechnisch fertig. Die Montage hat sehr viel Spaß gemacht und ist durch die Weiterentwicklung der Bausätze auch einfacher geworden. Jetzt sind die anderen zwei Wagenkästen dran. Sollte es da zu Besonderheiten kommen, berichte ich wieder davon. Interessanter wird es dann wieder beim Strahlen und Lackieren!
28. April 2020 Der fertige Wagen
Hier noch die Bilder des fertigen Wagens:
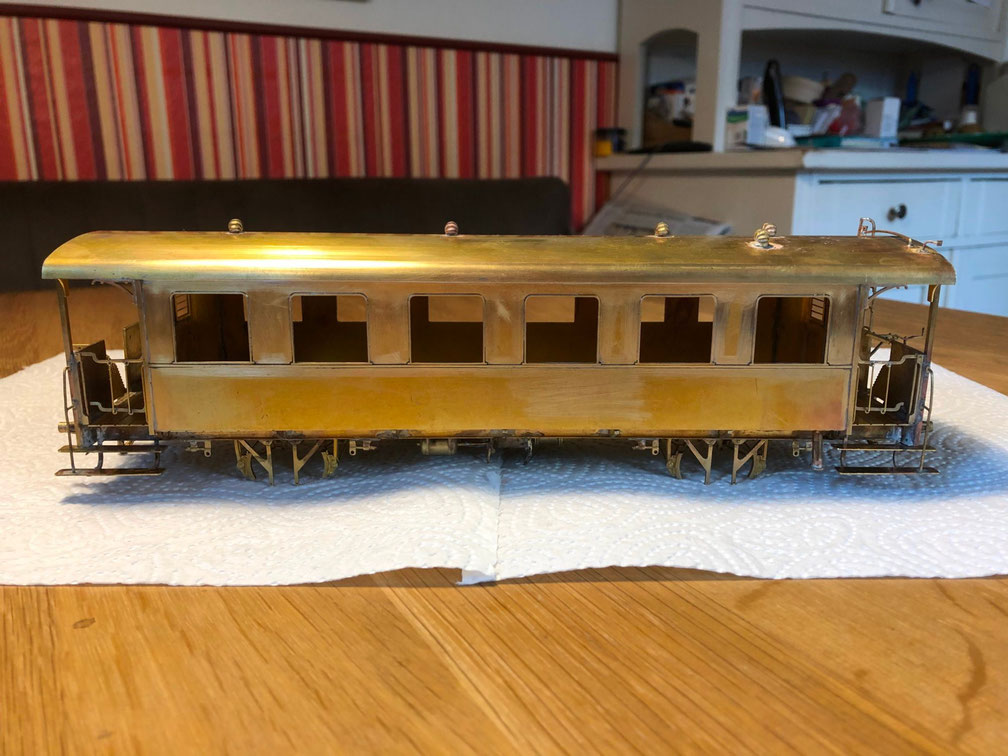
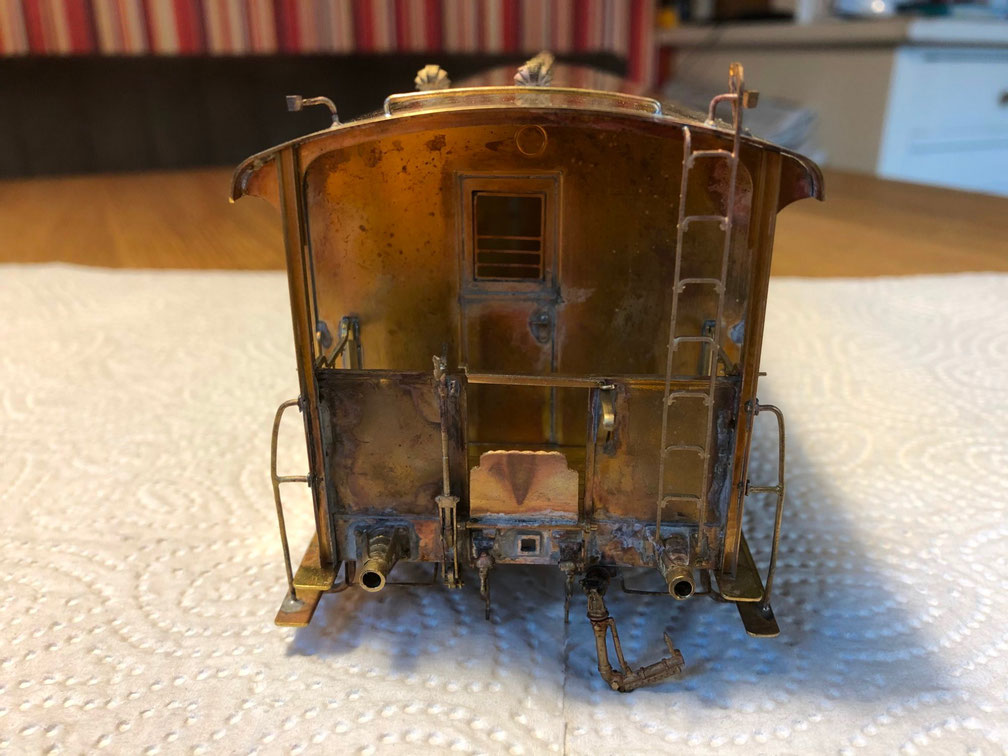
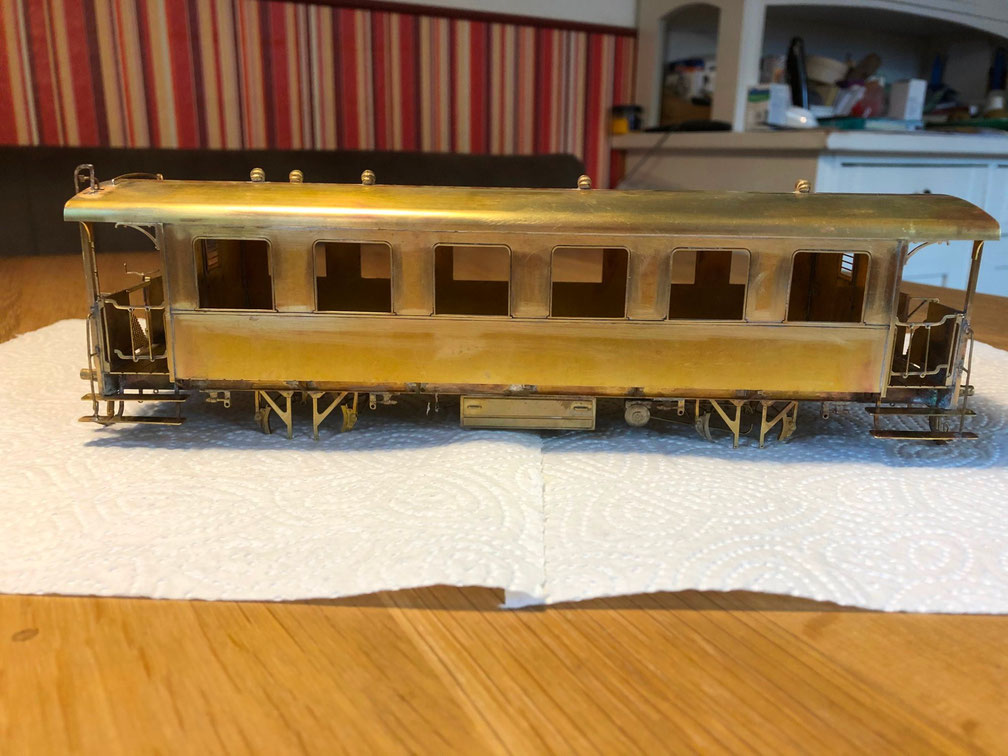
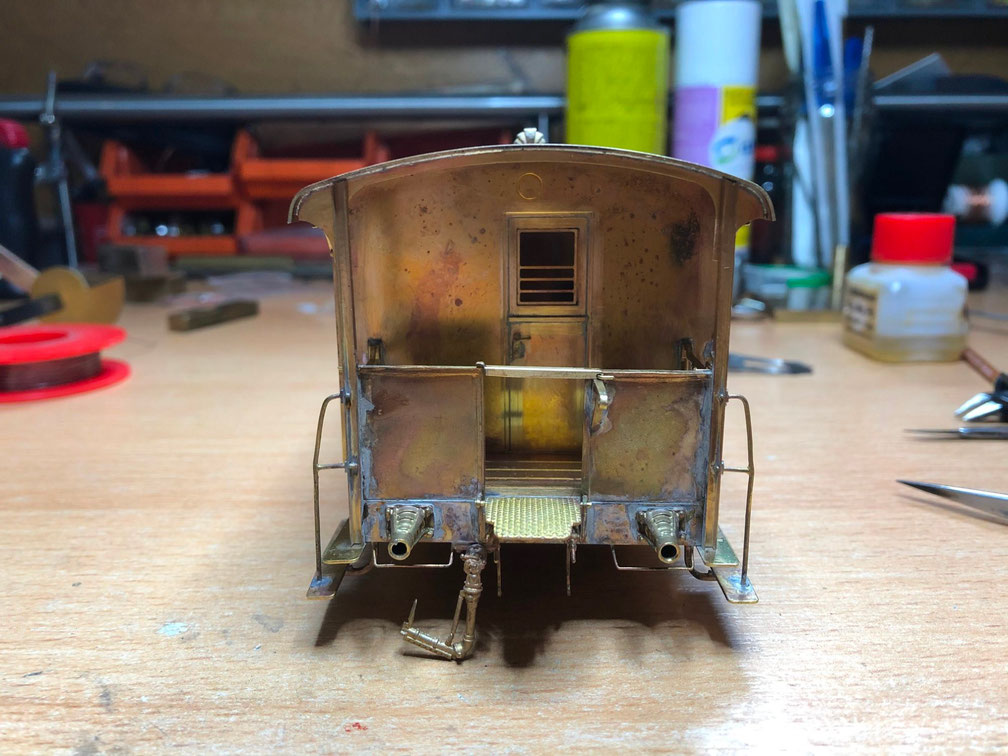
Auch in der Vitrine machen die Zwischenergebnisse noch ohne Federn und Achsen eine gute Figur, da steht ganz rechts auch noch das Erstlingswerk.
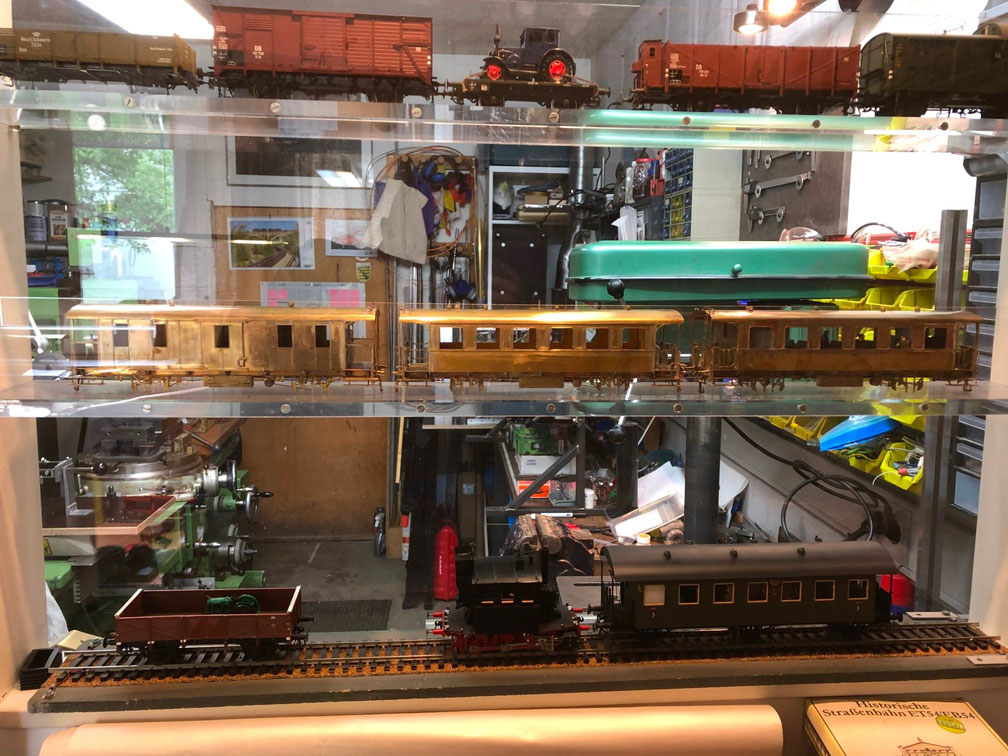
5. Mai 2020 Herausforderung Aufstiegsleiter
Hallo zusammen,
nach dem nun die ersten Wagen im "Rohbau" fertig sind, möchte ich über ein paar Spezialitäten und Änderungen in der Vorgehensweise bei den weiteren zwei CL14 berichten. Dazu gehört zweifellos die Aufstiegsleiter. Davon gibt es verschiedene Gussbäume, die aber meistens in der Stirnseitenansicht für Linksanschlag vorgesehen sind. Das Grundprinzip ist immer dass der Holm der Leiter zur Wagenaussenseite kürzer ist und unter dem Dach direkt befestigt wird, während der andere länger ist und einen Bogen als Geländer bildet, der dann mit einem Winkel abgestützt ist. Damit ihr seht was ich meine hier die Stirnwand des Pwl02:
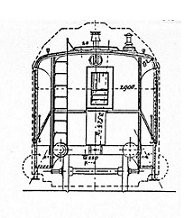
Zeichnung_Stirnseite_Pwl02 aus "Wagenverzeichnis KbStsB von 1913"
Und hier die des CL14 nach Blatt 548 aus "Wagenverzeichnis KbStsB von 1913"
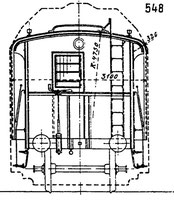
Zeichnung_Stirnwand_CL14 aus "Wagenverzeichnis KbStsB von 1913"
Jetzt kommt noch hinzu, dass die Leiter mal auf der Handbremsseite liegt, mal gegenüber. Das hat mich anfangs ein bisschen verwirrt, deshalb auch die Zeichnungen oben. Der Gußbaum in den CL14 Bausätzen sieht so aus:

Die beiden bezeichneten Teile werden benötigt, es liegt uns allerdings eine Leiter vor, die erst "CL14 tauglich" gemacht werden muss, weil der Holm mit dem Bügel auf die linke Seite gehört. Ich bin folgendermaßen vorgegangen:
Zuerst das Maß für den linken Holm ermitteln, der dann direkt unter dem Dach festgelötet wird. Hierbei einfach die Leiter an den Wagen halten, die unteren Enden der Holme sollten dabei mittig neben der Pufferhülse liegen. Dann habe ich eine Rundzange genommen und erst mal den Bogen am kurzen Holm in der richtigen Höhe abgerundet und den Rest des Holms abgeschnitten. Hierbei ist der Holm angebrochen, das kann natürlich nicht so bleiben. Daher muss das mit etwas Hartlot stabilisiert werden:
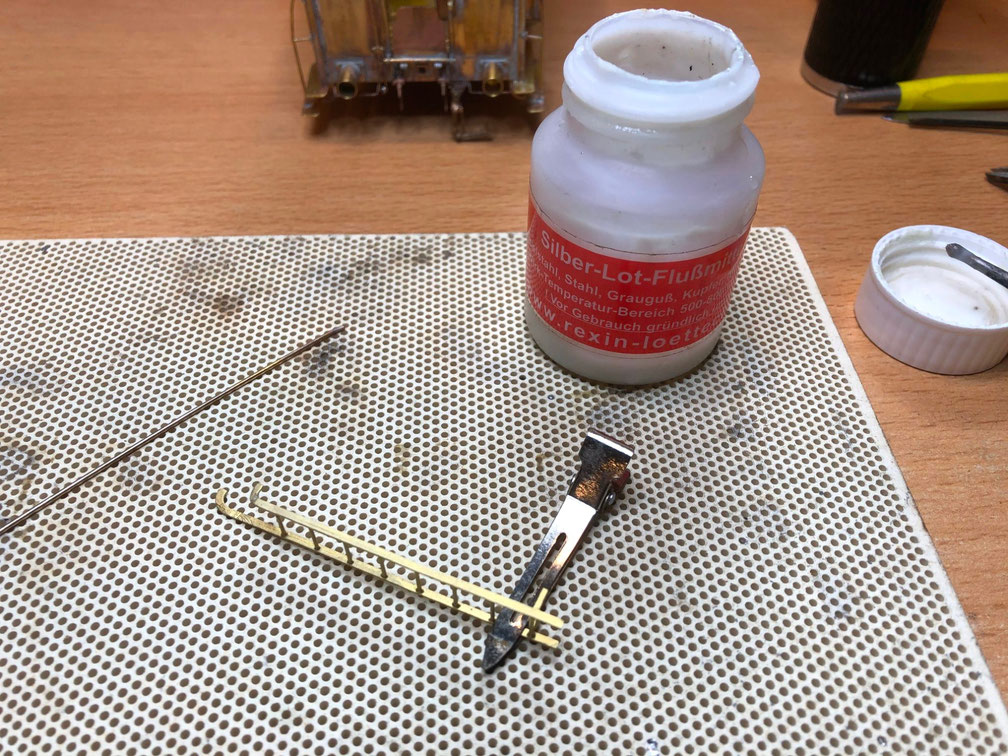
Bei vorsichtigem Gebrauch des Silberlots sieht es dann so aus:
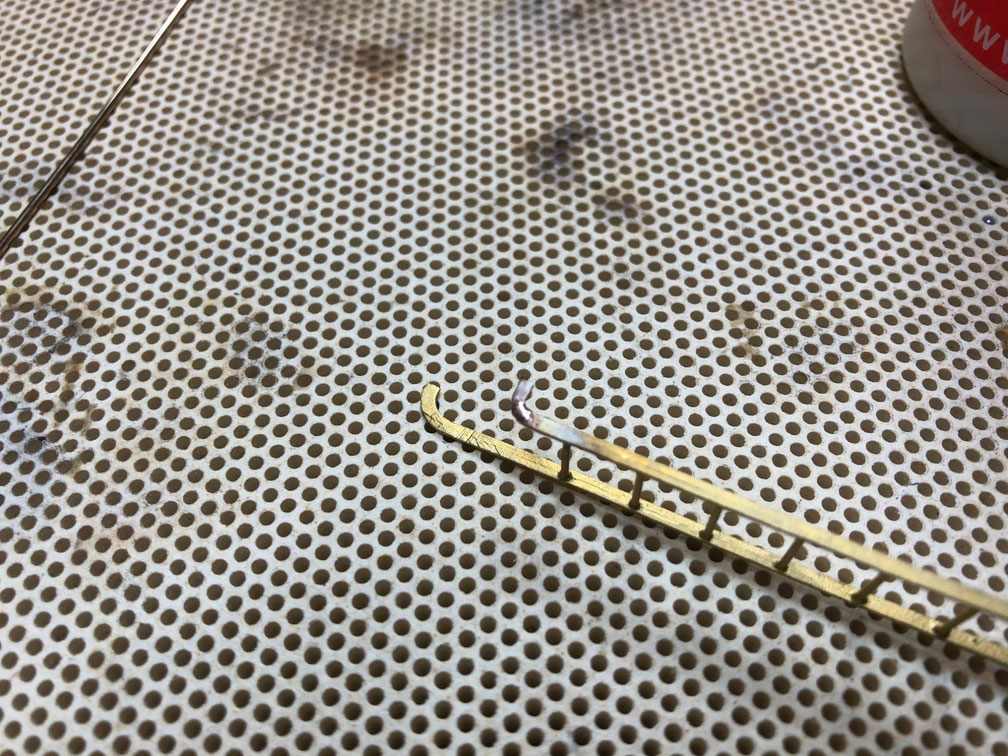
Wenn der Klecks etwas zu groß ist, kann man den ohne weiteres mit der Schlüsselfeile versäubern.
Jetzt kann man den linken Holm ggf. anpassen und das Anlöten des Befestigungswinkels (ebenfalls mit Hartlot) vorbereiten. Hier muss man sich aus geeigneten Reststücken von Material eine oft etwas abenteuerliche Haltevorrichtung bauen. Meine sah so aus, erfüllte aber den Zweck:
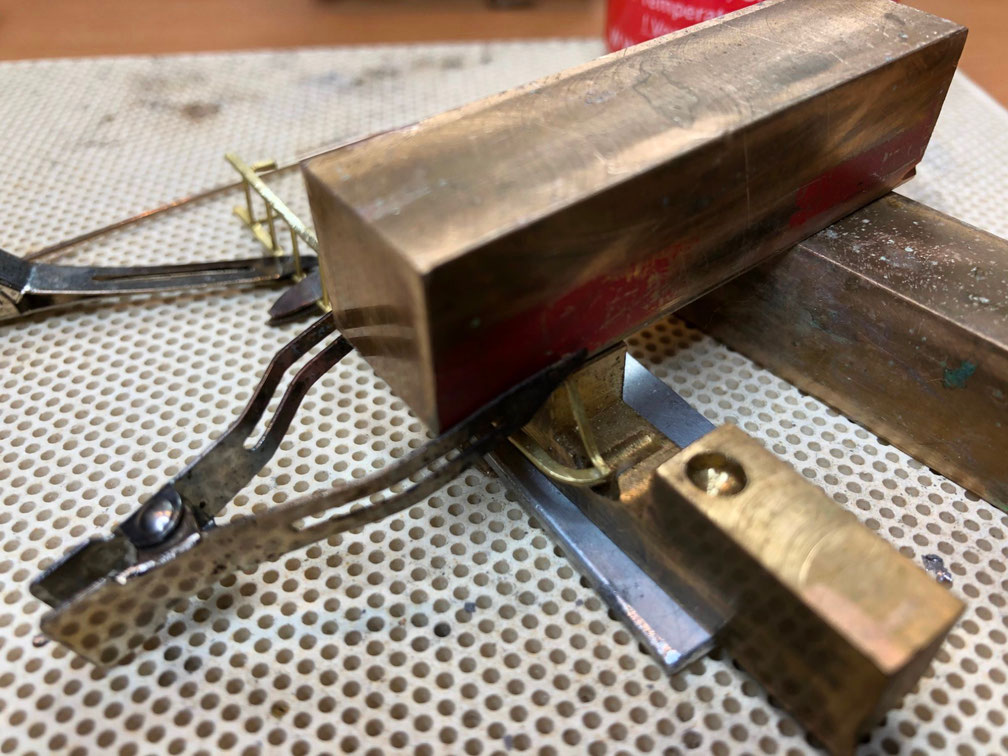
Fertig versäubert kann das Ergebnis dann so aussehen:
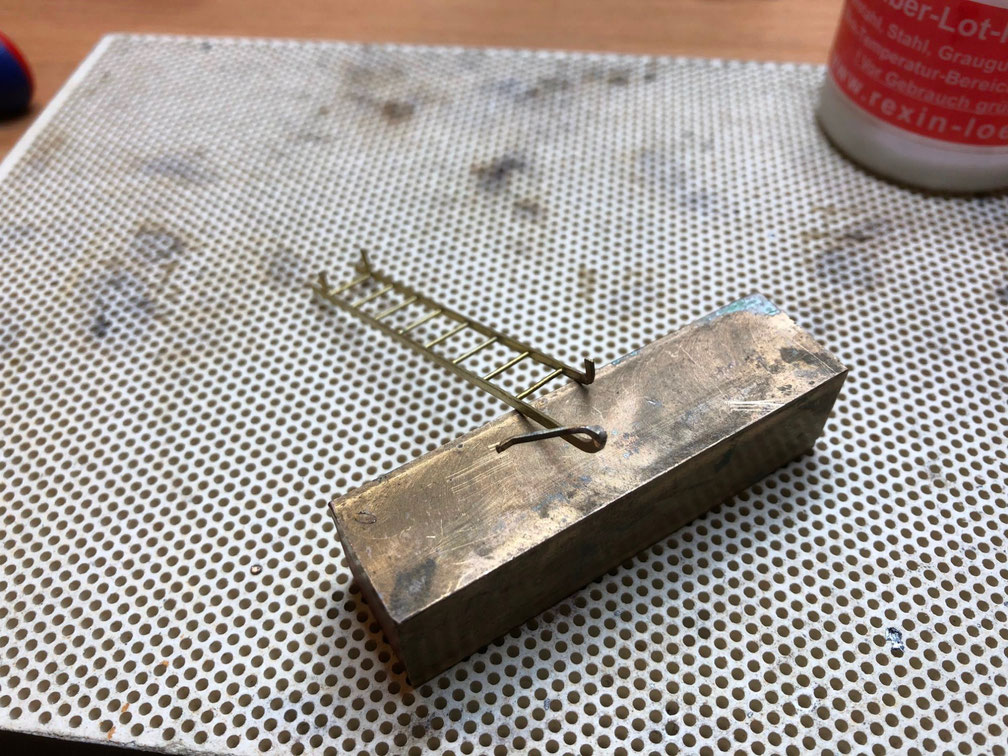
Jetzt sollte man noch die beiden unteren Halter auf Festigkeit überprüfen. Bei einer meiner Leitern war einer nicht sehr stabil, daher habe ich auch hier eine Verstärkung durch etwas Hartlot vorgenommen. Es wäre ja schade, wenn der Halter bei der Lackiervorbereitung oder bei der Reinigung abfallen würde.
Damit hat man die Leiter fertig angepasst und kann die Leiter am Dach festlöten:
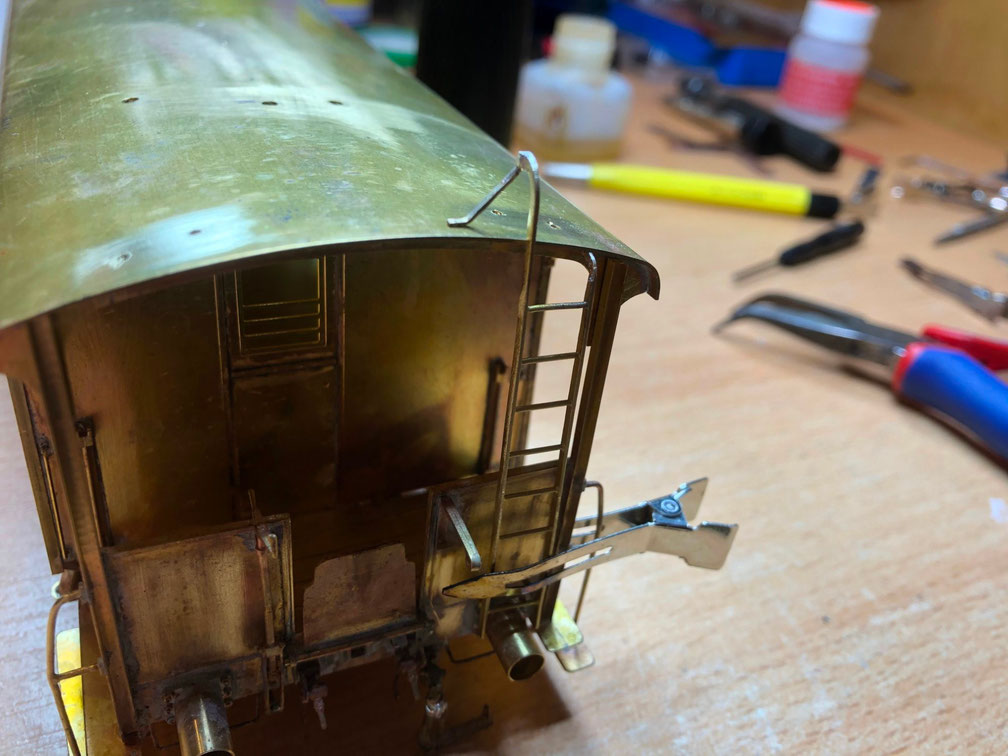
Ich löte hierbei erst den kurzen Holm unter dem Dach an und überprüfe die Lage der Leiter. Dann kann man noch evtl. Korrekturen des Befestigungswinkels vornehmen und die Leiter ist schon mal fixiert.
Das war's. Also - keine Angst vor dem Hartlöten und dem Verändern von Teilen! Nicht immer haben wir im Modellbau Idealbedingungen in Form von sofort passenden Gussteilen. Gerade die fast unglaubliche Vielfalt bei den Lokalbahnwagen stellt uns hier immer wieder auf die Probe.
5. Mai 2020 Problembehebung Bodenplatte
Hallo zusammen,
Heute mal ein Bericht über ein Missgeschick und seine Behebung:
Als ich den Wagenkasten von Wagen 3 das erste Mal auf das Fahrgestell gelegt habe, bin ich fast vom Stuhl gefallen. Das Bodenblech war ca. 1,5mm schief auf das Chassis aufgelötet das war mir bis jetzt noch nicht aufgefallen! Ursache: Ich hatte mich beim Auflöten auf die äußeren Wagenkastenstützen verlassen, einer hatte jedoch ein anderes Abstandsmaß zum Längsträger.
Was tun? Abfeilen des Überstandes und in Kauf nehmen des Spalts auf der anderen Seite? Das wäre Pfusch!
Also gab es keine andere Möglichkeit als das Bodenblech wieder abzulöten, Chassis und Bodenblech vom Lötzinn zu reinigen und neu aufzulöten. Gott sei Dank habe ich die Bodenbleche nur an den Längsträgern festgelötet, so konnte ich das Fahrgestell auf den Kopf und damit auf die Plattformstützen stellen, das Bodenblech von unten her erhitzen, von oben etwas Druck auf die jeweilige Lötstelle ausüben und so Stück für Stück die Lötung wieder lösen:
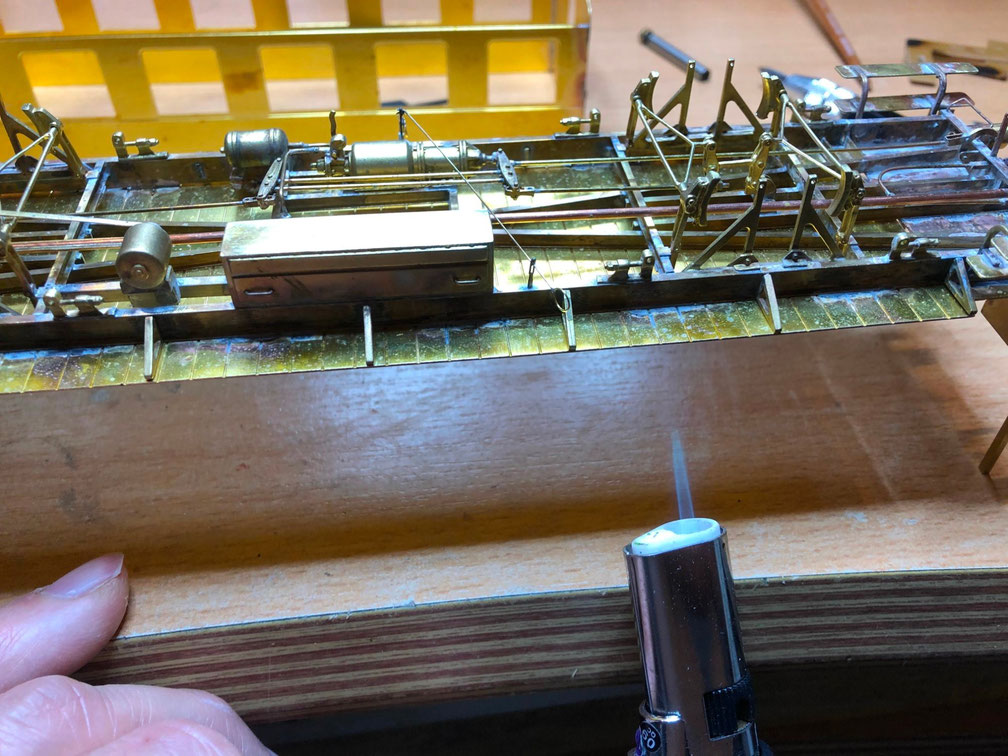
Es haben sich auch keine Anbauteile des Unterbodens gelöst, ich konnte die Lötwärme recht gut dosieren. Das Reinigen des Bodenblechs von den Lötzinnresten war dann noch eine umfangreiche Aktion, aber wenn man das Bodenblech diesmal richtig verlöten will, muss das weg! Ein Schaber hat hier gute Dienste verrichtet, das Neuverlöten ist dann ohne weiteres von statten gegangen und der Wagen konnte ordnungsgemäß fertiggestellt werden:
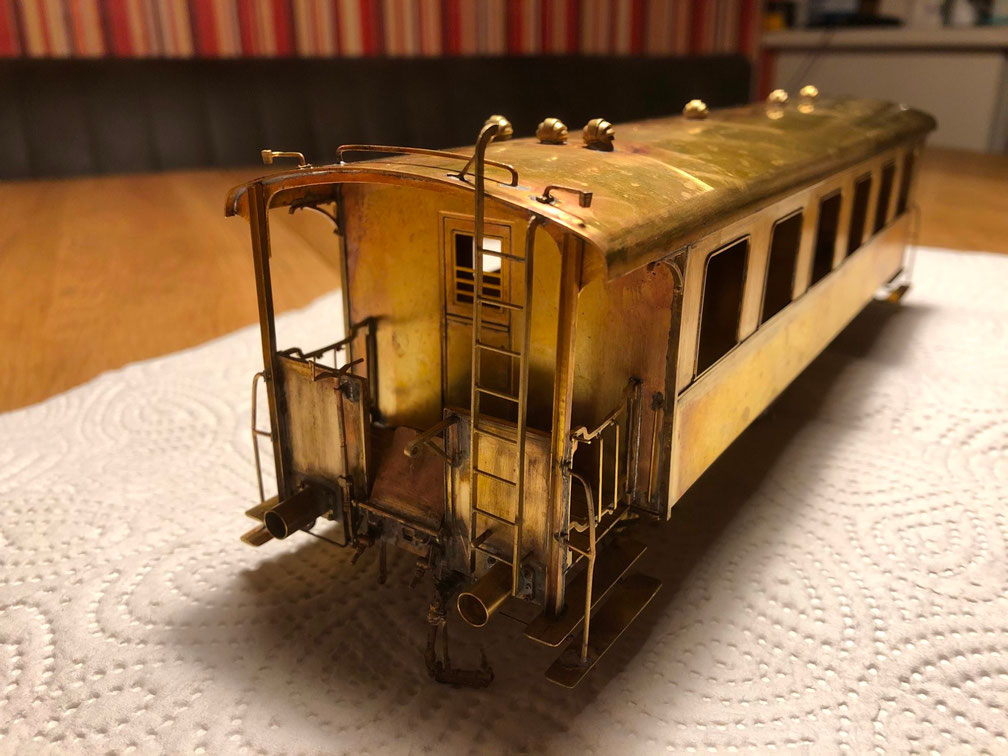
Wie man sieht, geht nicht immer alles klar, aber meistens gibt's auch eine Lösung!
5. Mai 2020 Veränderte Vorgehensweisen
Hallo zusammen,
Bei den letzten beiden Wagen sind aus der Erfahrung mit den schon fertigen ein paar Veränderungen im Ablauf eingeflossen. Als erstes das Anlöten der Wagenkasten-seitigen Auflagen für die Plattformgitter. Diese Teile gehören meiner Meinung nach zu den am Schwierigsten zu befestigenden Teilen. Warum? Zum Einen wegen der hohen Temperatur, die nötig ist um diese Teile gleichzeitig mit dem dünnen Blech der Stirnwände auf Löttemperatur zu bringen und zum Anderen wegen der etwas zu groß geätzten Mulde in der Stirnwand. Wenn man einen Spalt zwischen der Auflage und der Stirnwand vermeiden will, muss man mit Zinn auffüllen und nachher mehr oder weniger versäubern. Das läßt sich am fast fertigen Wagenkasten nur mit großen Schwierigkeiten bewerkstelligen, daher habe ich diese Teile diesmal gleich am Anfang an die Stirnwände angelötet.
Das Ganze stellt sich so dar:
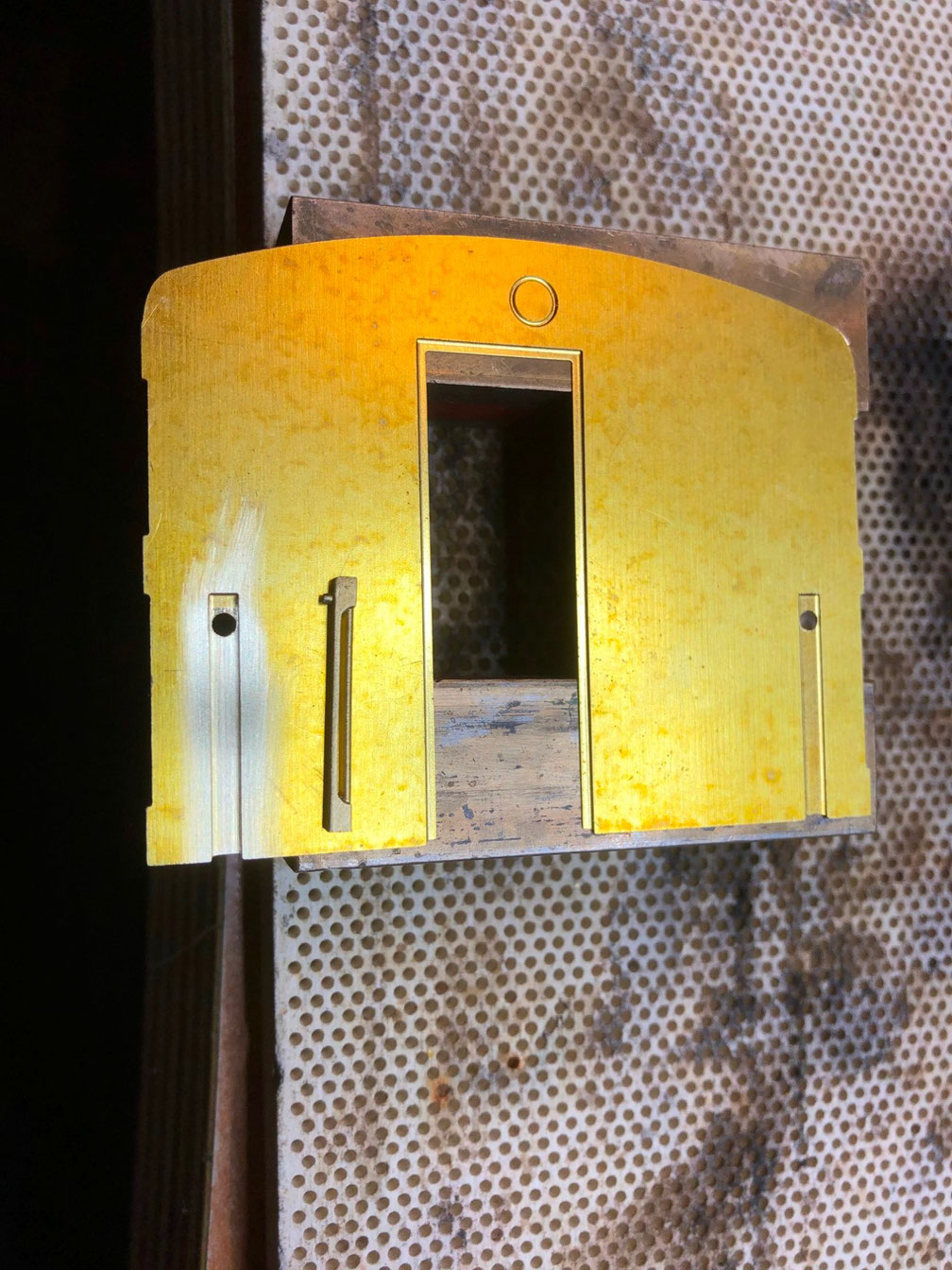
Werner Scholze warnte mich auch vor, dass bei dieser Ätzblech-Serie die Bohrung, die für den angegossenen Stift auf der Rückseite der Gitterauflage vorgesehen ist, um 0,5mm zu niedrig ist. Daraufhin habe ich mir überlegt, wie ich da vorgehe. Es gab drei Möglichkeiten:
- Die 1mm Bohrung nach oben zu erweitern
- Die Bohrung einfach mit 1,9mm aufzubohren und so den Versatz nach oben zu ermöglichen (siehe Foto oben)
- Den Stift wegfeilen und so anzulöten
Aufgrund der Ergebnisse beim Testen habe ich beim Rest der Wagen Möglichkeit 3 für die beste erklärt. Aber nun zurück zum Festlöten. Mit meiner "Lötzinn-Auflage-Methode" bin ich hier nicht weitergekommen. Zu oft ist das Lot auf dem Stirnwand-Blech geschmolzen und nicht in den Spalt gelaufen:
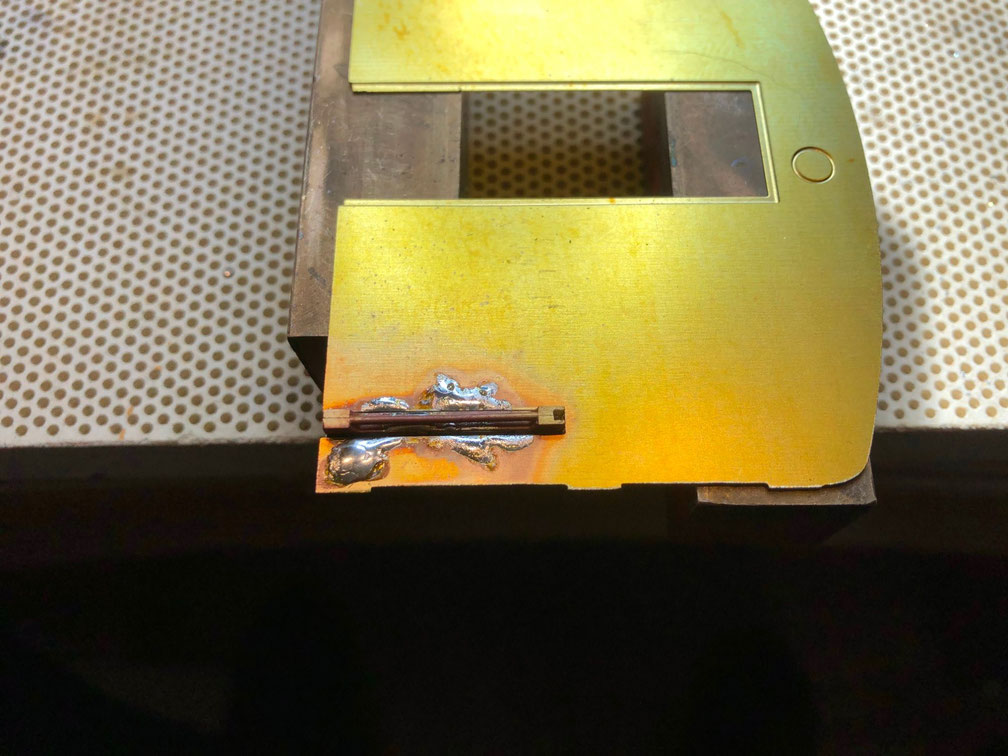
Da ist man dann eine zeitlang beschäftigt, das Zeug wieder von der Stirnwand wegzubekommen!
Ich musste also die Teile soweit erhitzen, dass ich das Lötzinn an den heißen Teilen zum Schmelzen bringen konnte und damit dann gezielt mit dem Lötdraht den Spalt gefüllt habe. Ohne Finisharbeiten geht das aber auch nicht ab. Das Ergebnis sieht dann auf jeden Fall viel besser aus:
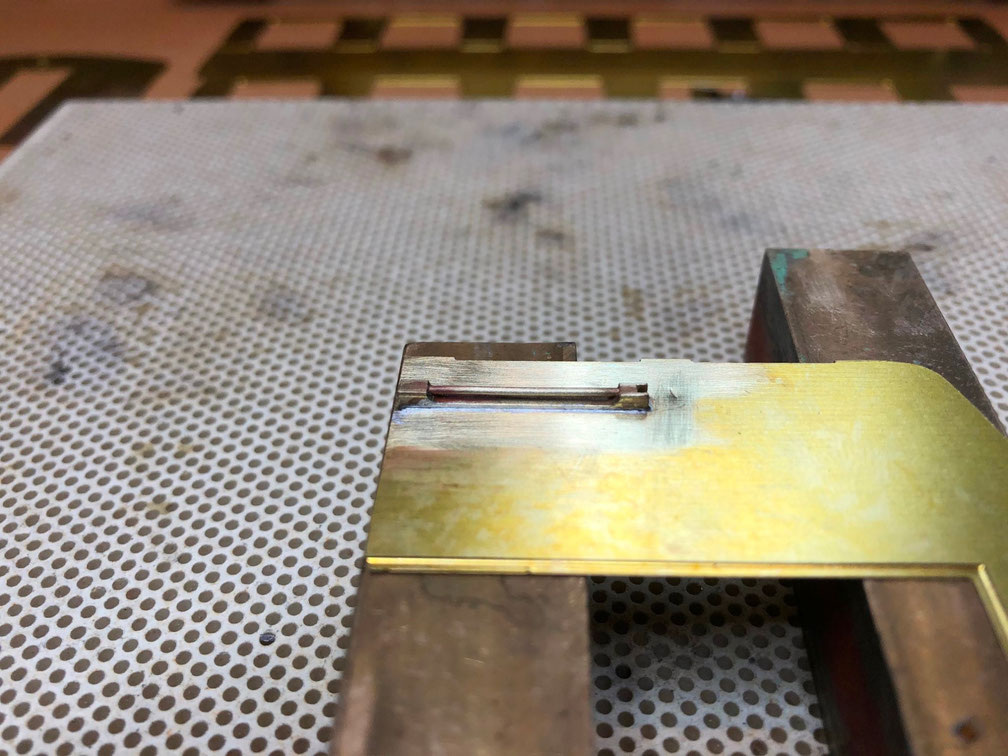
Das wäre so am fast fertigen Wagenkasten nicht möglich gewesen! In der Folge hat sich gezeigt, dass die Lötung auch bei den Arbeiten zum Erstellen des Wagenkastens nicht mehr aufgegangen sind. Diese Vorgehensweise hat sich also bewährt. Vielleicht kann der eine oder andere von euch auf diese Erfahrung zurückgreifen. Die Teile sind ja auch an den vierfenstrigen Lokalbahnwagen dran. Mir graust's jetzt schon davor!!
5. Mai 2020 Der Karosseriebau ist abgeschlossen!
Hallo zusammen,
gestern Abend habe ich es geschafft: Die vier Wagen sind im Rohbau fertiggestellt und mein Erstlingswerk mit allen neuen Features nachgezogen!
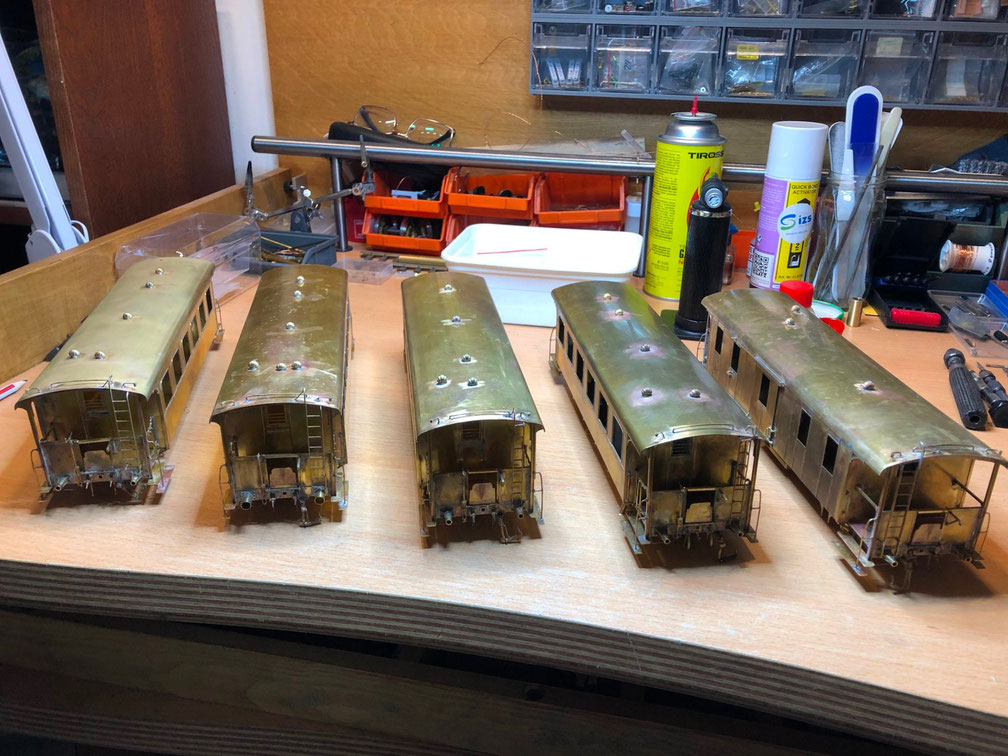
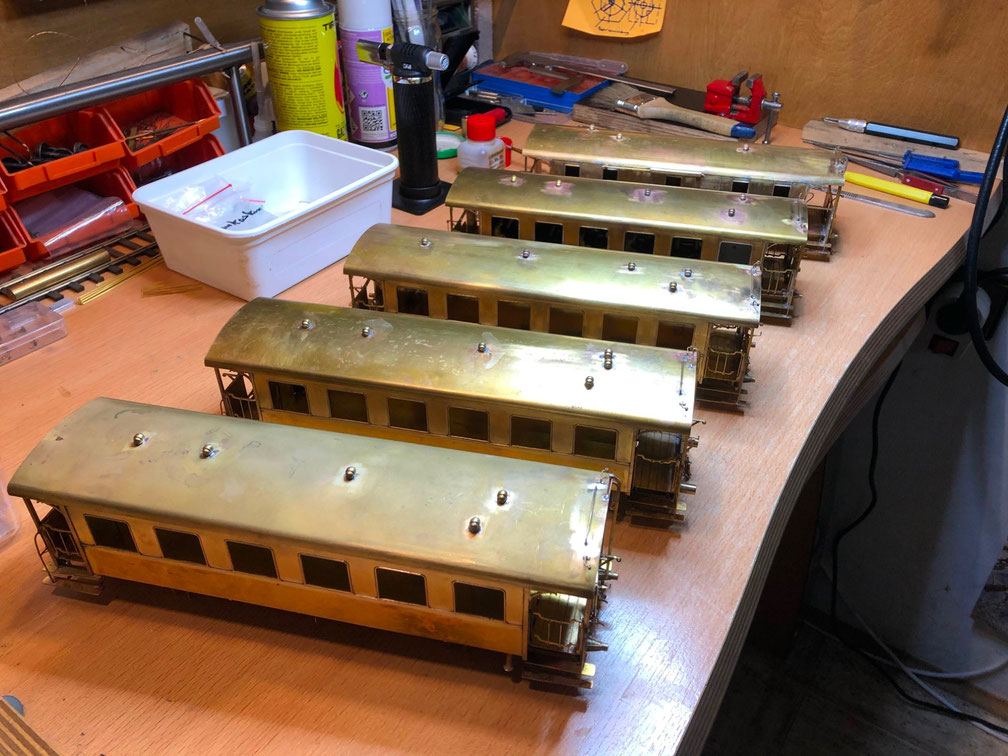
Langsam werde ich zum Lokalbahnwagen-Spezialist. Nun freue ich mich aber auf die nächsten Arbeitsschritte strahlen und lackieren. Zwischendrin werde ich mich dann auch um die Inneneinrichtung der Wagen kümmern. Die besteht aus Polystyrol-Platten für Boden und Wände und die bekannten Bänke aus Kunststoff. Materialmäßig ist also bei dieser Bauaktion für jeden was dabei.
Kommentar schreiben